Eliminate delays, shutdowns and waste so you can boost profitability!
When you’re pushing hard to keep up with the global demand for steel, you can’t allow unexpected shutdowns, equipment failure and runaway waste to slow you down. If you can’t maintain an efficient flow of raw material – including coal, iron ore, coke and limestone – production drops, along with revenues. At the same time, your costs go up due to unscheduled maintenance, inefficient energy use, safety issues and more, which squeezes profits from both sides.
Forty years ago, there were only eight countries capable of producing more than 10 million metric tons of steel per year. In 2014, there were 18 countries that produced that much steel, which means your competition can come from anywhere in the world. All it takes is a mistracked conveyor assembly or an accumulation of fugitive material to force you to shut down operations, especially on older conveyor equipment. Even fugitive dust can cause a plant shutdown for health and safety reasons.
Solving problems with durable, effective solutions.
The equipment we manufacture at Martin Engineering is designed to keep materials moving efficiently, quickly and safely throughout your plant. At every key point in the process, starting when the raw material is unloaded from the ship or railcar, our products help you maximize efficiency as material travels through a complex system of conveyors that connect sintering kilns and coke ovens to the blast furnace, basic oxygen furnace or electric arc furnace. We provide durable, effective solutions that clean conveyor belts thoroughly and eliminate carryback. Plus, our transfer point and flow aid products keep material moving through chutes and hoppers and prevent it from sticking to the interior walls of your kilns and silos. And we have the most effective solutions on the market for containing and filtering dust.
At Martin, we stand behind our products. We have steel customers all over the world who are using our products to keep materials and product moving every day! We want you to be as confident in our material handling products as our existing customers are, and that’s why we back our equipment with a 100% Money-Back Guarantee.
Over seven decades, we’ve built a worldwide reputation for solving our customers’ problems in the steel industry. That means whatever your biggest challenge is, we’ve probably seen it before and already come up with a solution that works. So give us a call and let one of our highly experienced engineers apply their expertise to your business.
- Keep downtime for conveyor belt maintenance and belt cleaning to a minimum
- Move material more efficiently along conveyor systems
- Reduce spillage and equipment damage by keeping conveyor belts aligned
- Manage airborne dust and minimize the risk of explosion and inhalation
- Prevent material from spilling off of moving conveyors
- Protect steel workers from extreme temperatures and moving equipment
- Deliver more steel by maximizing overall throughput
- Eliminate excessive downtime for maintenance and housekeeping
- Reduce costs by minimizing waste and reducing energy consumption
MartinPLUS® Maintenance Helps Steel Plant Overcome Regulatory Issues
Air Cannons Eliminate Production Bottlenecks at Steel Production Plant
Martin® Tracker™ Corrects Conveyor Belt Misalignment At Steel Complex
Tracker™ Installation Corrects Spillage and Fugitive Material
Industrial Vibrators And Air Cannons Clear Blockage In Hopper
Air Cannons Move Sticky Coal From Bins
Martin® Impact Cradles Boost Steel Production From 15% to 100%
Conveyor Guards Improve Worker Safety
Air Cannon Installation Results In 80% Fewer Stops For Cleanup
Martin® Belt Cleaner Makes Replacing Worn Blades Easier
CleanScrape® Belt Cleaner improves plant efficiency and profitability
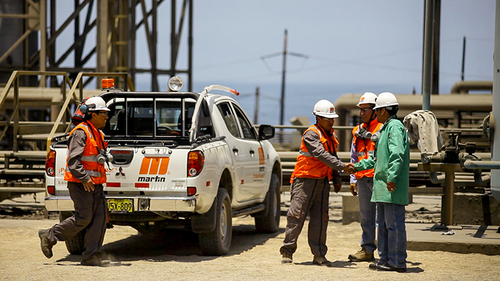
Free Engineering and Application Assistance
Our technicians have solved problems for people in your industry all over the world. Take advantage of our wealth of knowledge. Tell us about your situation today to learn how Martin can improve your performance, safety and bottom line - with no obligation. We want to ensure that you choose the right solution for your exact needs and we are willing to invest the time upfront to get it right the first time.
Briefly Describe Your Application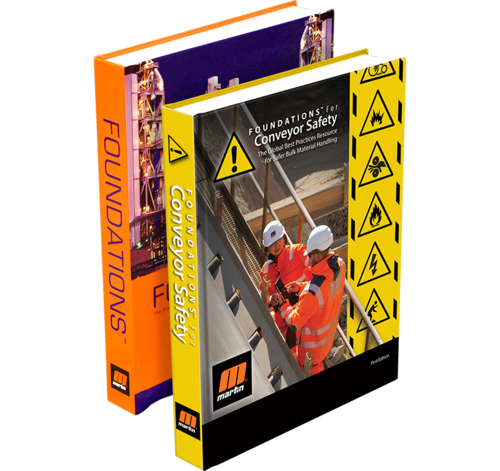
Foundations™ for Conveyor Safety
Learn to Calculate your Return on Conveyor Safety™ with our compilation of worldwide best practices for safer bulk material handling in this first-ever textbook dedicated exclusively to the safety of conveyor systems.
Request Your FREE PDF or Hard-Back Copy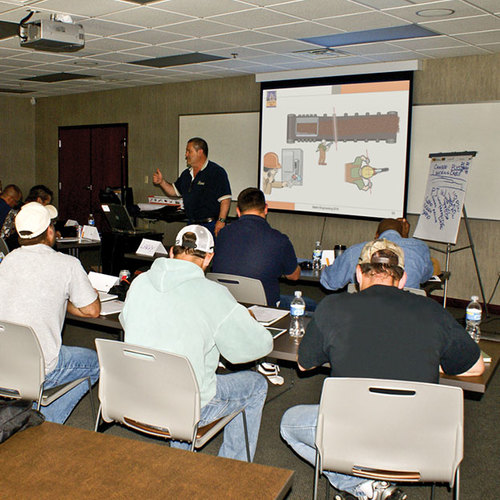
Train Your Personnel For Better Belt Conveyor Performance and Safety
Foundations™ Training workshops train your plant operating and maintenance personnel and engineers about belt conveyors – how they work and how to make them work better. From a Basic Introduction to belt conveyors and safety to an Advanced Training option for your skilled and experienced members, Martin will share our 70 years of experience and research with your team members. You can't afford not to educate your team with Martin!
Ask About Our On-Site and Online Options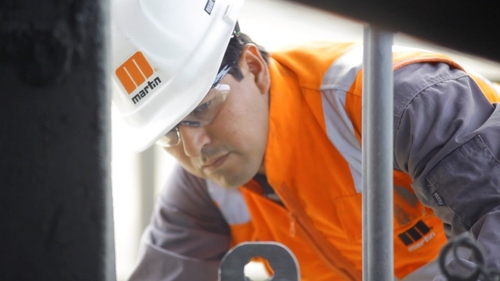
Save With Our Martin® Walk the Belt™ Service!
Every conveyor is different, even within the same facility! We can provide regularly-scheduled reviews of your bulk material handling system components, involving a specialized crew with the expertise necessary to achieve high operating standards, keeping the conveyor system running at maximum productivity. Immediate data and photos will be available to facility managers and our suggestions will ensure long-term savings and efficiency.
Get Your Belts Reviewed By People Who Know What They’re Looking At -- At No Charge!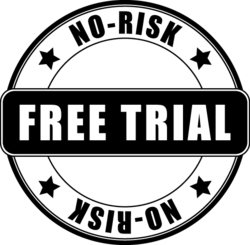
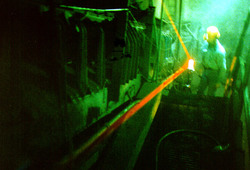
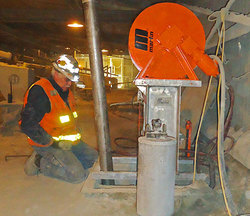