Products Used | Typhoon Air Cannon |
---|---|
Product Types Used | Air Cannons |
Industry | Coal-Fired Power |
Customer | NTPC Ltd., Rihand, Uttar Pradesh, India |
Problem
NTPC Ltd. was experiencing flow issues on the Selective Catalytic Reduction (SCR) reactor due to ash buildup. In a pilot project overseen by YARA Environmental Technologies, the SCR was installed on a trial basis with the intent to reduce NOx (nitrogen oxide) emissions. Talec Engineering Pvt. Ltd. was brought in to consult and install equipment. After installing an 18 in. (457 mm) isokinetic extraction duct for sampling purposes, the company discovered that ash carried with the hot flue gases passing through it would build and clog the duct. An access hole was bored in the reactor duct for manual cleaning, but due to high heat and harmful gas emissions, managers asked Talec to seek a safer and more effective solution.
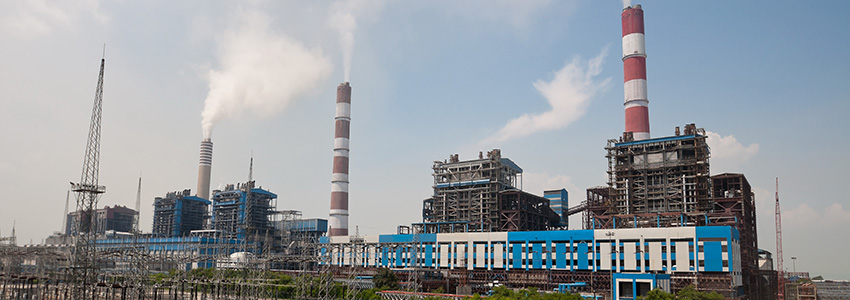
Solution
Talec Engineers asked Martin Engineering India to examine the situation and offer solutions. Technicians decided to install a 70-liter (18.5 gallon) Martin® Typhoon Air Cannon, installed using the existing access hole and connected to the plant's compressed air system. The cannon fires a blast of air up to 120 PSI (8.27 BAR) from a pressurized tank, through the straight pipe assembly and distributed at a downward angle. For easier and safer maintenance, the valve can be removed by a single worker in one easy step and replaced within minutes, without removing the tank. Fired from a control room or manually from a nearby panel, the cannon mitigates buildup in the duct for more efficient flow.
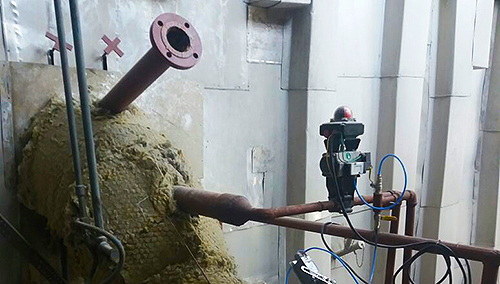
Result
After two months of operation, those close to the project report that the flow through the catalyst has greatly improved. With an available firing sequence as frequent as every minute, controllers are able to monitor minor fluctuations in flow efficiency and address them right away. In addition, workers no longer have to manually clean the catalyst and risk exposure to super heated flue gas. "Safety is critical, and we are very happy with this solution," said an operator. "The improvement to efficiency exceeded our expectations." Following a successful trial run of the pilot project, NTPC Ltd. intends to add a similar solution in other locations.
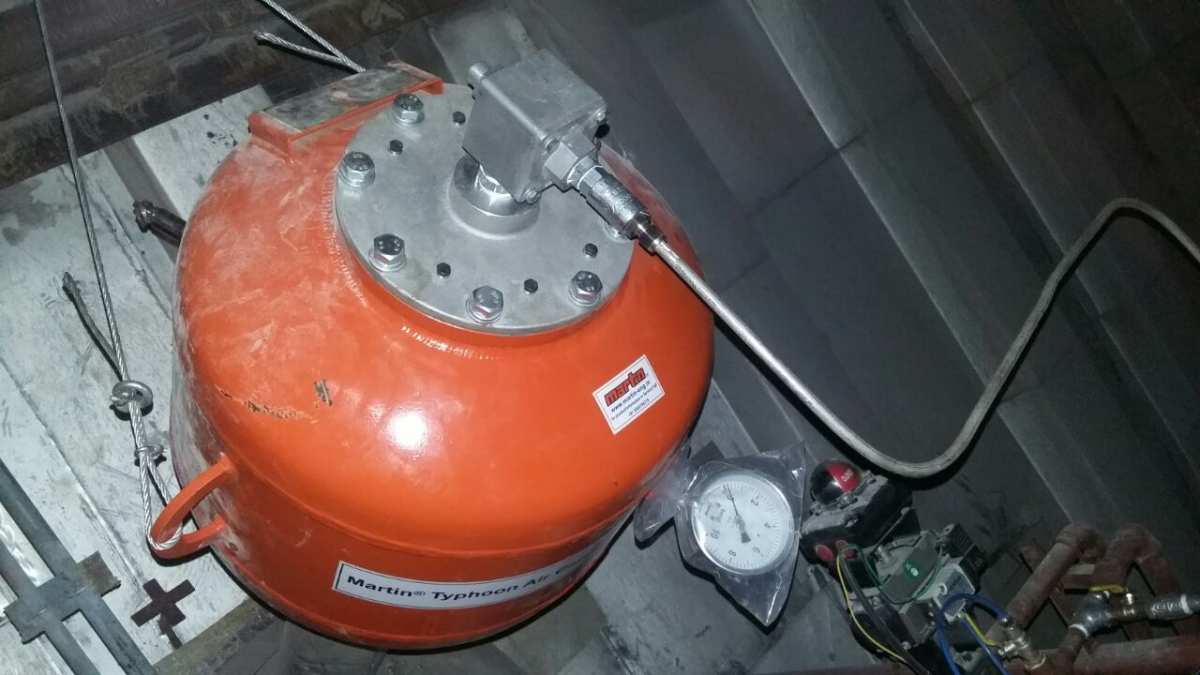